钢轨探伤检测
发布时间:2025-04-03
钢轨探伤检测是保障铁路运输安全的核心技术环节,通过系统化评估钢轨表面及内部缺陷状态,预防疲劳裂纹、核伤等隐患。检测需重点关注材料连续性损伤、几何尺寸异常及环境腐蚀影响,采用超声波、电磁感应等无损技术实现精准定位与定量分析。
注意:因业务调整,暂不接受个人委托测试望见谅。
检测项目
钢轨探伤核心检测项目包含五大类:
表面裂纹及剥离缺陷:重点识别轨头工作面横向裂纹、轨腰纵向裂纹及轨底锈蚀扩展裂纹
内部疲劳损伤:探测轨头核伤、轨腰水平裂纹等隐蔽性缺陷
焊接接头质量:评估闪光焊、铝热焊等接头区域的未熔合、气孔及夹杂物
轨头廓形磨损:测量磨耗量超过3mm的廓形畸变区域
螺栓孔裂纹:检查接头夹板区域应力集中导致的放射状裂纹
检测范围
探伤作业覆盖全路网不同工况区段:
正线轨道:包括直线段、曲线段(半径≤800m重点加密检测)
道岔区域:尖轨、辙叉心等关键部件的疲劳损伤监测
桥梁隧道段:特殊环境下钢轨的应力腐蚀开裂评估
新轨验收:出厂钢轨的内部夹杂物与残余应力检测
服役周期监测:按UIC标准划分的周期性预防性检测
检测方法
主流探伤技术体系包含四类方法:
超声波脉冲反射法:采用0°直探头(2-5MHz)检测垂直缺陷,70°斜探头探测横向裂纹
涡流检测技术:适用于表面及近表面缺陷的高速扫查(最高5km/h)
磁粉探伤法:对轨底边缘裂纹进行荧光磁粉可视化处理
激光超声检测:非接触式测量薄层剥离缺陷(精度达0.1mm)
相控阵技术:多角度电子扫描实现复杂缺陷三维成像
检测仪器
标准化探伤设备配置包含:
多通道数字超声仪:至少具备8通道同步采集能力(A扫+B显模式)
轮式探头阵列:集成45°、70°组合探头组(频率2.25MHz±10%)
电磁涡流仪:配备差分式矩形探头(频率100kHz-1MHz可调)
钢轨轮廓测量仪:激光位移传感器精度±0.02mm
数据采集系统:满足EN标准的数据存储与波形回放功能
耦合剂自动供给装置:维持探头与轨面间稳定水膜层(厚度0.3-0.5mm)
专业探伤作业需严格执行TB/T 2340标准要求,采用双机交叉验证模式确保缺陷检出率≥98%。针对时速350km以上高速铁路区段,应配置动态补偿系统消除振动干扰,并建立基于大数据分析的钢轨健康度预测模型。
检测服务范围
1、指标检测:按国标、行标及其他规范方法检测
2、仪器共享:按仪器规范或用户提供的规范检测
3、主成分分析:对含量高的组分或你所规定的某种组分进行5~7天检测。
4,样品前处理:对产品进行预处理后,进行样品前处理,包括样品的采集与保存,样品的提取与分离,样品的鉴定以及样品的初步分析,通过逆向剖析确定原料化学名称及含量等共10个步骤;
5、深度分析:根据成分分析对采购的原料标准品做准确的定性定量检测,然后给出参考工艺及原料的推荐。最后对产品的质量控制及生产过程中出现问题及时解决。
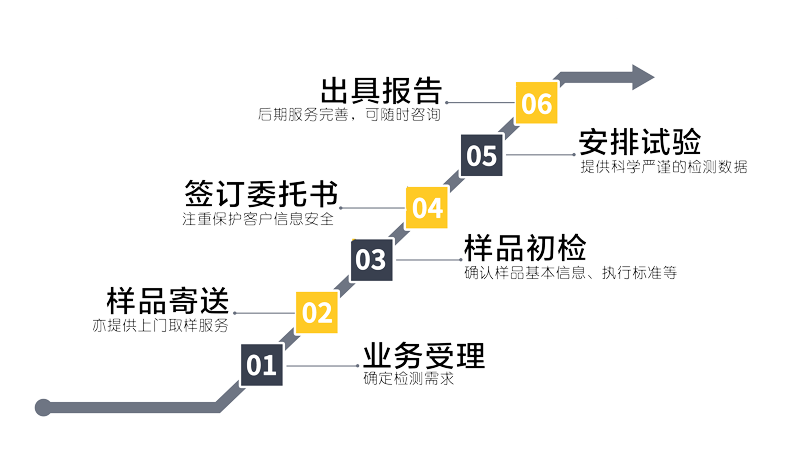
合作客户展示
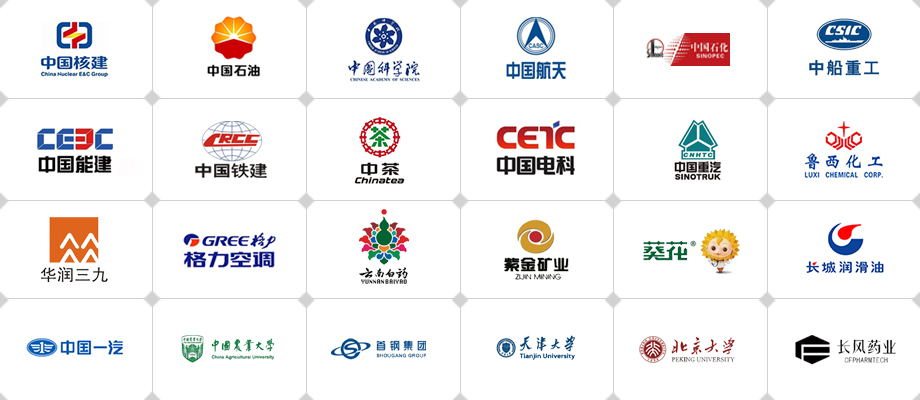
部分资质展示
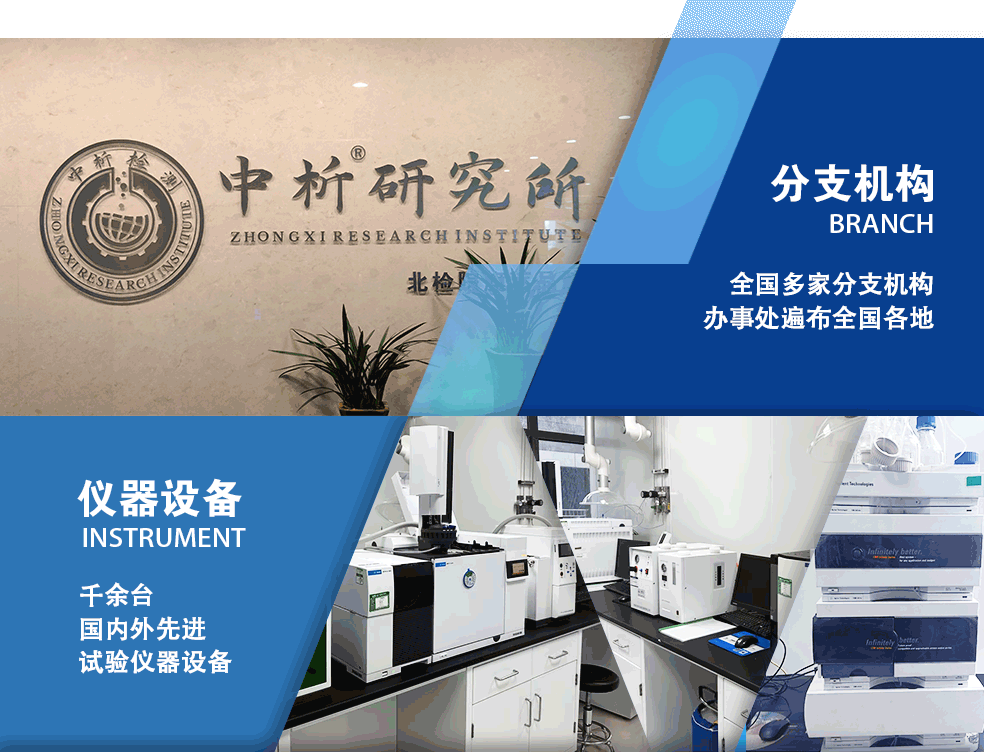