传动件检测
发布时间:2025-07-09
传动件检测是确保机械传动系统可靠性的核心技术环节,重点评估齿轮、轴承等关键部件的材料性能、几何精度及疲劳寿命。核心检测涵盖硬度梯度分析、微观组织表征、动态载荷模拟等专业领域,通过量化指标验证传动件在极端工况下的结构完整性和服役安全性。
注意:因业务调整,暂不接受个人委托测试望见谅。
检测项目
表面硬度检测:采用洛氏/维氏硬度计测定表层硬化深度,梯度测量精度±0.5HRC,硬化层深度范围0.1-5.0mm
齿形误差分析:通过齿轮测量中心评估渐开线偏差,检测精度0.5μm,涵盖压力角误差±0.1°及齿距累积误差≤6级
金相组织检验:依据GB/T13298进行显微组织评级,识别碳化物形态(1-6级)及晶粒度(4-12级)
扭矩疲劳试验:动态加载测试系统模拟实际工况,频率范围5-50Hz,循环次数≥10⁷次,扭矩波动控制±1%
磁粉探伤检测:检测表面裂纹缺陷,灵敏度可识别0.02mm×15mm线性缺陷,符合ISO4987标准
残余应力分析:X射线衍射法测定表层应力分布,测量深度0.05-0.5mm,精度±20MPa
尺寸形位公差:三坐标测量机检测同轴度≤0.01mm,圆柱度≤0.005mm,平面度≤0.003mm
材料成分光谱:直读光谱仪测定合金元素含量,C/S/P等元素检出限0.001%,分析时间≤30秒
表面粗糙度:轮廓仪测量Ra值范围0.05-10μm,评定长度5倍取样长度
盐雾腐蚀试验:按GB/T10125执行中性盐雾测试,持续时长48-1000小时,评级方法ISO10289
耐磨性试验:摩擦磨损试验机模拟工况,载荷范围50-2000N,滑动速度0.1-5m/s
冲击韧性测试:夏比冲击试验温度-196℃至室温,能量分辨率0.1J,试样尺寸10×10×55mm
检测范围
齿轮传动组件:涵盖渐开线圆柱齿轮/锥齿轮/蜗轮的齿面接触疲劳强度验证
滚动轴承系统:检测滚道表面剥离、保持架变形及游隙变化等失效模式
联轴器部件:评估弹性元件疲劳寿命及金属部件过载变形量
传动轴类零件:检测扭转刚度及临界转速下的共振特性
链轮链条系统:验证销轴磨损量及链板拉伸强度
同步带传动:测定橡胶基材老化系数及玻纤线绳抗拉强度
液压传动元件:柱塞泵摩擦副表面镀层结合力检测
风电齿轮箱:行星轮系微点蚀及剥落损伤分析
汽车变速箱:换挡拨叉磨损量及同步齿环锥度检测
工程机械履带:链节销孔配合间隙及表面硬化深度控制
机器人减速器:谐波齿轮柔轮应力集中系数测定
航空航天传动:涡桨发动机齿轮渗碳层梯度控制检测
检测标准
ISO6336齿轮承载能力计算标准
ASTME384显微硬度测试规范
GB/T3077合金结构钢技术条件
ISO10825齿轮磨损与点蚀评定准则
AGMA2001齿轮胶合承载能力计算
GB/T3480.5圆柱齿轮接触强度校核
ISO281滚动轴承额定寿命计算
ASTME606应变控制疲劳试验
GB/T6398金属材料疲劳裂纹扩展速率
ISO683热处理钢金相检验通则
DIN3990齿轮强度计算规范
GB/T11345焊缝无损检测等级分类
检测仪器
齿轮测量中心:配备三维扫描测头,实现齿形/齿向/齿距误差全参数分析,最小分辨率0.1μm
高频疲劳试验机:液压伺服系统提供±250kN动态载荷,频率范围0.1-300Hz,用于传动轴扭振疲劳测试
扫描电子显微镜:背散射电子探测器观察磨损表面形貌,配合EDS分析微区成分,放大倍数10-500,000×
X射线应力分析仪:采用Cr-Kα辐射源,ψ角法测定齿轮根部残余应力,测量深度0.1mm
直读光谱仪:氩气环境激发光源,同时分析C、Cr、Mo等15种元素,分析精度±0.005%
三维表面轮廓仪:白光干涉技术测量齿面粗糙度,纵向分辨率0.01nm,评定参数Ra/Rz/Rsm
微机控制扭转试验机:最大扭矩20kN·m,转角分辨率0.001°,用于花键轴静扭强度验证
高温摩擦磨损试验机:环境温度范围RT-800℃,模拟变速箱同步环工况,记录摩擦系数变化曲线
检测服务范围
1、指标检测:按国标、行标及其他规范方法检测
2、仪器共享:按仪器规范或用户提供的规范检测
3、主成分分析:对含量高的组分或你所规定的某种组分进行5~7天检测。
4,样品前处理:对产品进行预处理后,进行样品前处理,包括样品的采集与保存,样品的提取与分离,样品的鉴定以及样品的初步分析,通过逆向剖析确定原料化学名称及含量等共10个步骤;
5、深度分析:根据成分分析对采购的原料标准品做准确的定性定量检测,然后给出参考工艺及原料的推荐。最后对产品的质量控制及生产过程中出现问题及时解决。
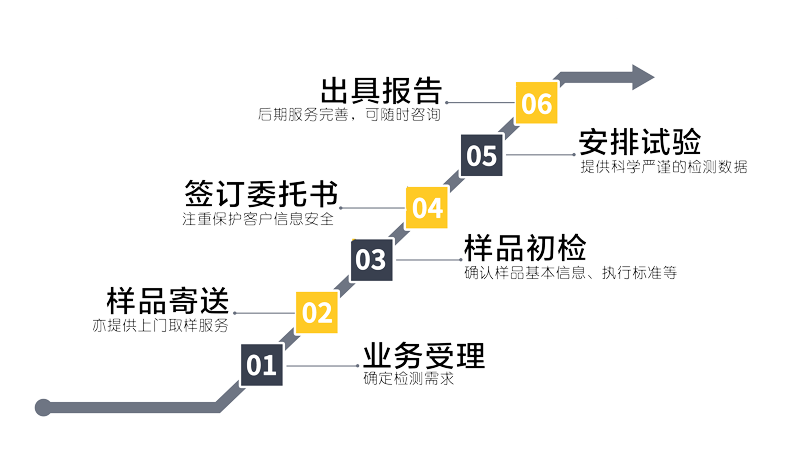
合作客户展示
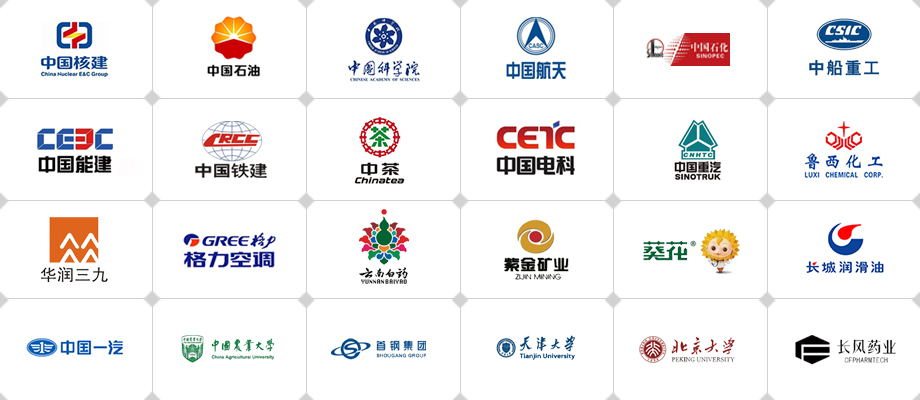
部分资质展示
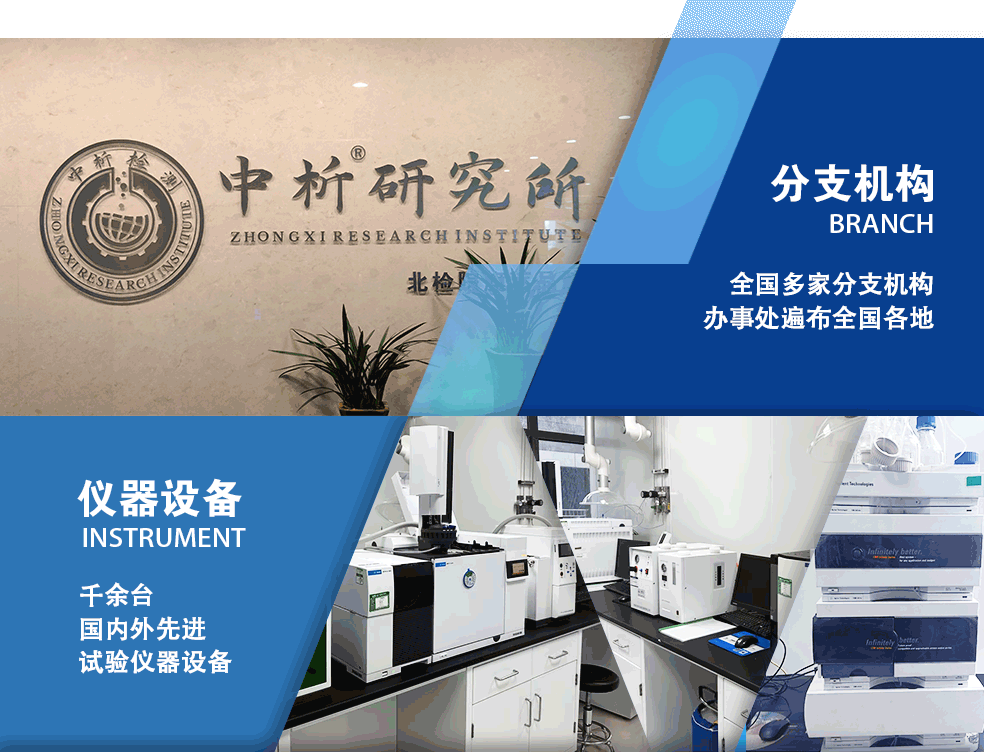