球磨机检测
发布时间:2025-04-19
球磨机检测是保障设备安全运行与工艺稳定性的关键环节,需通过系统性评估机械性能、磨损状态及运行参数实现精准诊断。核心检测项目涵盖筒体厚度、齿轮啮合精度、轴承温度与振动频谱分析等指标,需结合国家标准与行业规范进行科学评价。本文从技术角度阐述检测流程要点与实施方法。
注意:因业务调整,暂不接受个人委托测试望见谅。
检测项目
球磨机核心检测项目包含六大类:
结构完整性检测:筒体壁厚测量(允许误差±0.5mm)、端盖法兰平面度(≤0.1mm/m)、衬板固定螺栓预紧力(按设计值±5%)
传动系统评估:大齿轮径向跳动(≤0.15mm/m)、小齿轮轴向窜动(≤0.3mm)、联轴器对中偏差(轴向≤0.05mm/径向≤0.1mm)
轴承状态监测:轴瓦间隙(顶隙0.15-0.25mm/侧隙0.08-0.12mm)、润滑油膜厚度(≥25μm)、温升梯度(连续运行≤65℃)
动态特性分析:临界转速验证(工作转速≤75%临界转速)、振动烈度(空载≤4.5mm/s/负载≤7.1mm/s)、相位角一致性(相邻测点偏差<15°)
电气系统测试:电机三相电流不平衡度(≤10%)、绕组绝缘电阻(≥100MΩ)、启动转矩匹配性(110%-150%额定转矩)
工艺性能验证:研磨介质填充率(28%-32%有效容积)、物料粒度分布(D90偏差≤5%)、单位能耗比(kW·h/t)
检测范围
完整检测范围覆盖设备全生命周期:
新机验收阶段:基础沉降量(72小时观测<0.5mm/m)、空载试车振幅(轴向≤0.8mm/径向≤1.2mm)
定期维护周期:衬板磨损量分级评估(Ⅰ级<15%/Ⅱ级15%-30%/Ⅲ级>30%)、篦板缝隙扩大量(原始值+2mm为警戒值)
故障诊断过程:齿轮接触斑点分析(齿高≥45%/齿长≥60%)、轴承故障频率识别(BPFO/BPFI特征频率偏差>10dB)
改造验证测试:新型衬板安装间隙(周向3-5mm/轴向8-12mm)、变频改造后转矩波动率(≤5%)
特殊工况监测:低温环境启动力矩补偿值、高湿度工况绝缘性能衰减率
检测方法
标准化检测方法体系包含:
超声波脉冲反射法:采用5MHz探头测量筒体壁厚,设置V声程校正模式消除曲率误差
激光对中技术:应用CCD阵列传感器实现三维空间对中测量,分辨率达0.001mm
振动频谱分析法:设置1024线分辨率采集加速度信号,应用包络解调技术提取轴承故障特征
热成像诊断法:使用非制冷焦平面探测器捕捉温度场分布,温差>15℃判定异常发热点
油液铁谱分析法:通过直读式铁谱仪测定磨损颗粒浓度指数(WPC),建立PQ指数趋势模型
动态扭矩测试法:安装遥测扭矩仪实时记录传动轴扭矩波动曲线,采样频率≥5kHz
检测仪器
专业检测仪器配置方案:
数字超声波测厚仪:配备曲面自适应探头组(2MHz/5MHz/10MHz),支持B扫描成像功能
多通道振动分析系统:集成ICP加速度传感器(频响0.5Hz-15kHz),具备阶次跟踪与瀑布图分析模块
激光对中仪系统:含二维PSD位置传感器与自动计算软件包,测量距离可达20m
红外热像仪设备:384×288像素非制冷微测辐射计,热灵敏度<50mK@30℃
油液分析工作站:包含旋转式铁谱仪、粘度自动测定仪及颗粒计数器三位一体系统
无线扭矩测试系统:基于Zigbee传输协议实现多轴同步测量,量程范围±500Nm至±200kNm可选配
三维激光扫描仪:用于大齿轮齿形误差测量,点云密度达到0.01mm精度级
检测服务范围
1、指标检测:按国标、行标及其他规范方法检测
2、仪器共享:按仪器规范或用户提供的规范检测
3、主成分分析:对含量高的组分或你所规定的某种组分进行5~7天检测。
4,样品前处理:对产品进行预处理后,进行样品前处理,包括样品的采集与保存,样品的提取与分离,样品的鉴定以及样品的初步分析,通过逆向剖析确定原料化学名称及含量等共10个步骤;
5、深度分析:根据成分分析对采购的原料标准品做准确的定性定量检测,然后给出参考工艺及原料的推荐。最后对产品的质量控制及生产过程中出现问题及时解决。
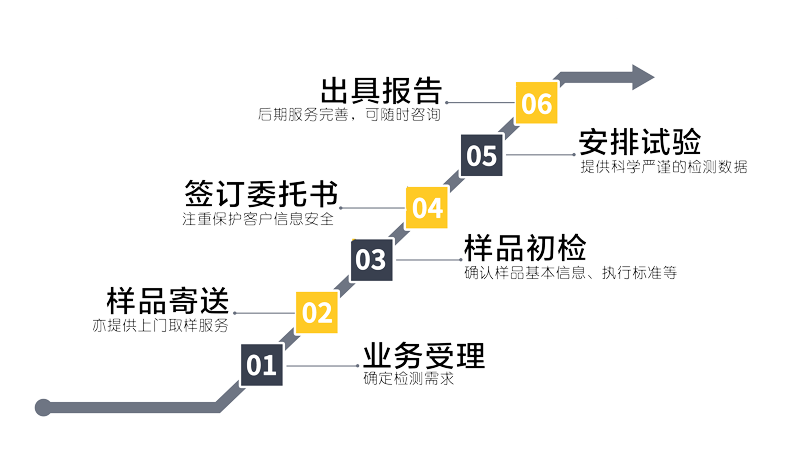
合作客户展示
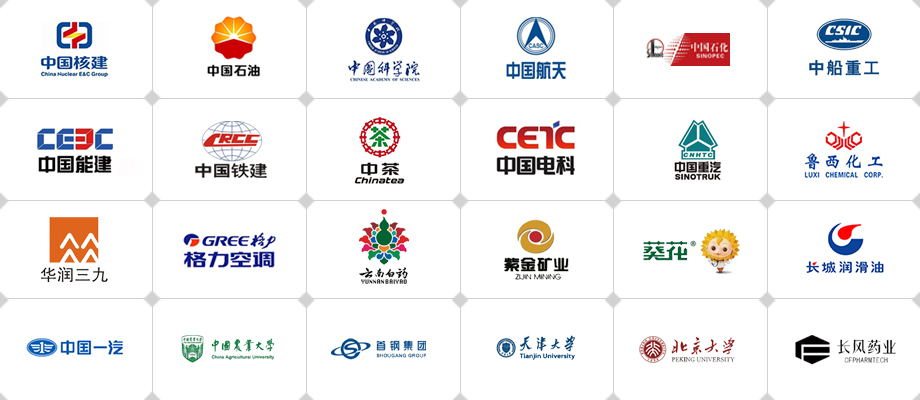
部分资质展示
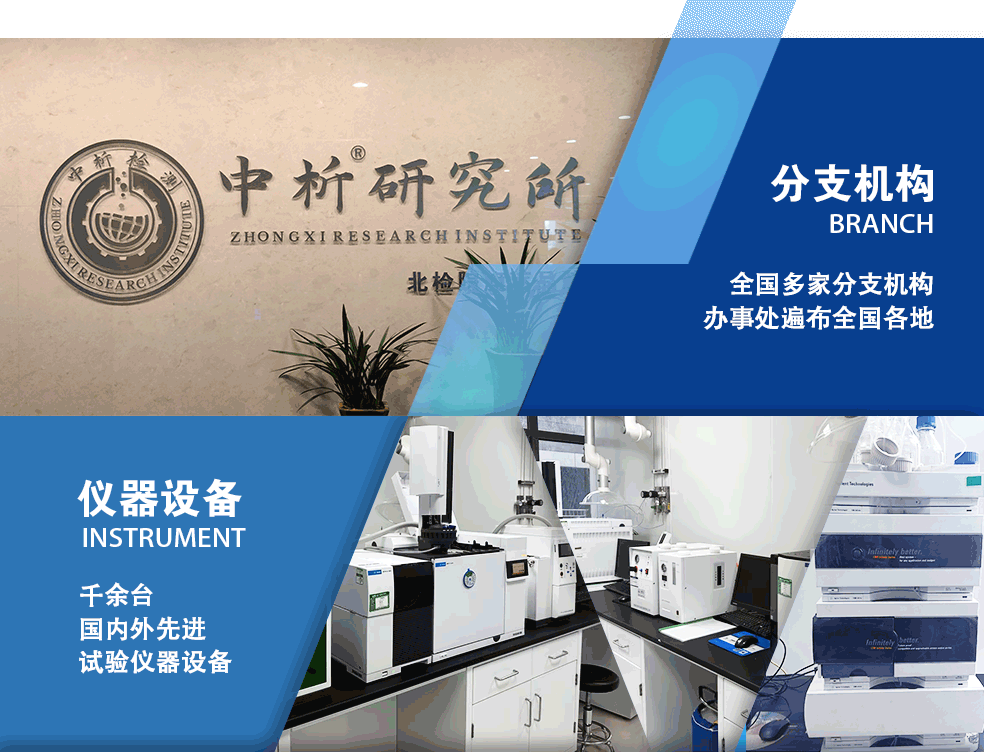