轨道磨损状态检测
发布时间:2025-05-09
轨道磨损状态检测是保障轨道交通系统安全运行的重要技术手段。本文系统阐述轨道几何尺寸、表面损伤、材料性能等核心检测项目,重点分析接触式测量、非接触扫描、材料分析等专业方法的应用规范,并介绍激光轮廓仪、超声波探伤仪等精密仪器的技术参数与操作标准。
注意:因业务调整,暂不接受个人委托测试望见谅。
检测项目
轨道磨损状态检测包含三大核心项目:几何参数测量、表面缺陷诊断和材料性能评估。几何参数测量涵盖轨头宽度、轨高、垂直磨损量等12项关键尺寸指标;表面缺陷诊断包括鱼鳞纹、剥离掉块、波磨等典型损伤形态的识别与量化;材料性能评估涉及硬度梯度测试、金相组织分析和残余应力测定。
1. 几何尺寸偏差:轨距角磨损量超过1.5mm需预警;垂直磨耗达到10%标称高度应启动更换程序;轨面不平顺度采用0.02mm精度标准
2. 表面损伤分级:依据TB/T 2344标准将裂纹深度分为Ⅰ级(<0.5mm)、Ⅱ级(0.5-1.5mm)、Ⅲ级(>1.5mm);波磨波长在30-300mm范围内需进行频谱分析
3. 材料性能变化:轨面硬度下降超过HB50需重点监测;马氏体组织含量超过15%判定为异常;残余压应力低于-300MPa时预警疲劳风险
检测范围
本检测体系适用于铁路干线、城市轨道交通、工矿企业专用线等不同场景的钢轨状态评估。具体包括:
1. 铁路运营线路:涵盖时速120-350km/h各等级线路的定期巡检与专项检测
2. 道岔关键区域:尖轨、辙叉部位的接触疲劳与塑性变形专项检测
3. 曲线路段:半径小于800m弯道的侧磨与轨距扩大量化监测
4. 焊接接头:铝热焊、闪光焊接头的热影响区裂纹与硬度突变检测
5. 特殊环境段:隧道内腐蚀磨损、沿海盐雾侵蚀、高寒地区脆性断裂的专项评估
检测方法
采用多维度综合检测技术体系:
1. 接触式测量法:使用数显游标卡尺测量轨头宽度;电子水平仪测定轨道横向倾斜度;弦线法检测直线段平顺度
2. 光学扫描技术:激光轮廓仪实现0.05mm精度的三维形貌重建;高速线阵CCD采集动态轮轨接触图像
3. 超声波探伤:双晶探头进行表面裂纹探测(频率5MHz);相控阵技术实现焊缝内部缺陷三维成像
4. 电磁检测法:涡流传感器识别表面微裂纹(分辨率0.1mm);漏磁检测装置评估亚表面损伤深度
5. 材料分析法:显微维氏硬度计测试硬化层梯度;X射线衍射仪测定残余应力分布;扫描电镜进行断口形貌分析
检测仪器
标准配置设备包含五大类12种专业仪器:
1. 几何测量设备:手持式激光轮廓仪(测量范围±50mm)、数字轨距尺(精度±0.1mm)、全站仪(角精度1")
2. 表面检测仪器:便携式电子显微镜(放大倍数200X)、白光干涉仪(纵向分辨率1nm)、电磁超声探头组
3. 材料分析设备:显微硬度计(载荷范围10-1000gf)、X射线应力分析仪(测量深度0.1mm)、金相制样系统
4. 动态监测装置:车载式轨道巡检系统(最高采样频率10kHz)、分布式光纤应变传感器(空间分辨率1m)
5. 数据处理终端:轨道状态大数据分析平台(支持TB级数据存储)、三维可视化诊断软件(符合EN 13848标准)
检测服务范围
1、指标检测:按国标、行标及其他规范方法检测
2、仪器共享:按仪器规范或用户提供的规范检测
3、主成分分析:对含量高的组分或你所规定的某种组分进行5~7天检测。
4,样品前处理:对产品进行预处理后,进行样品前处理,包括样品的采集与保存,样品的提取与分离,样品的鉴定以及样品的初步分析,通过逆向剖析确定原料化学名称及含量等共10个步骤;
5、深度分析:根据成分分析对采购的原料标准品做准确的定性定量检测,然后给出参考工艺及原料的推荐。最后对产品的质量控制及生产过程中出现问题及时解决。
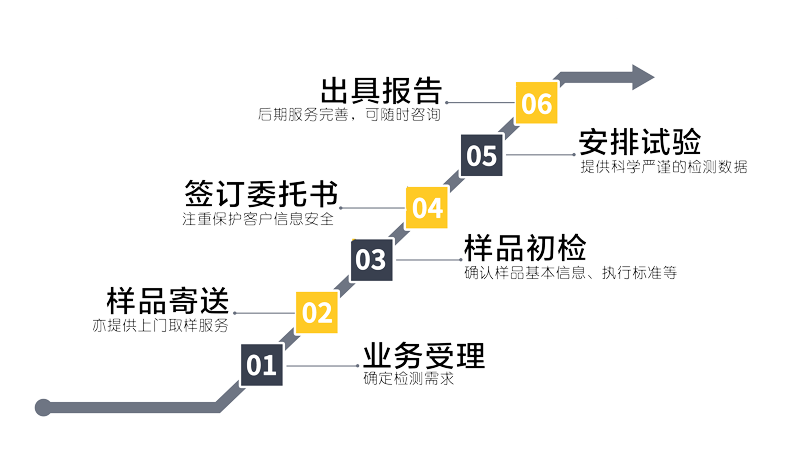
合作客户展示
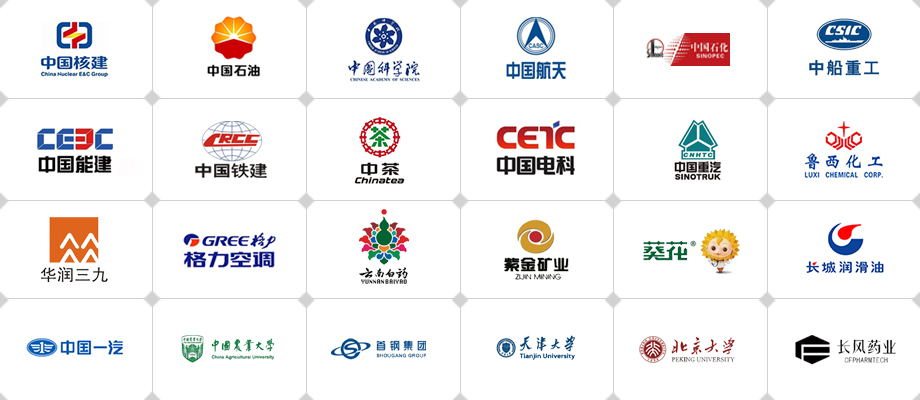
部分资质展示
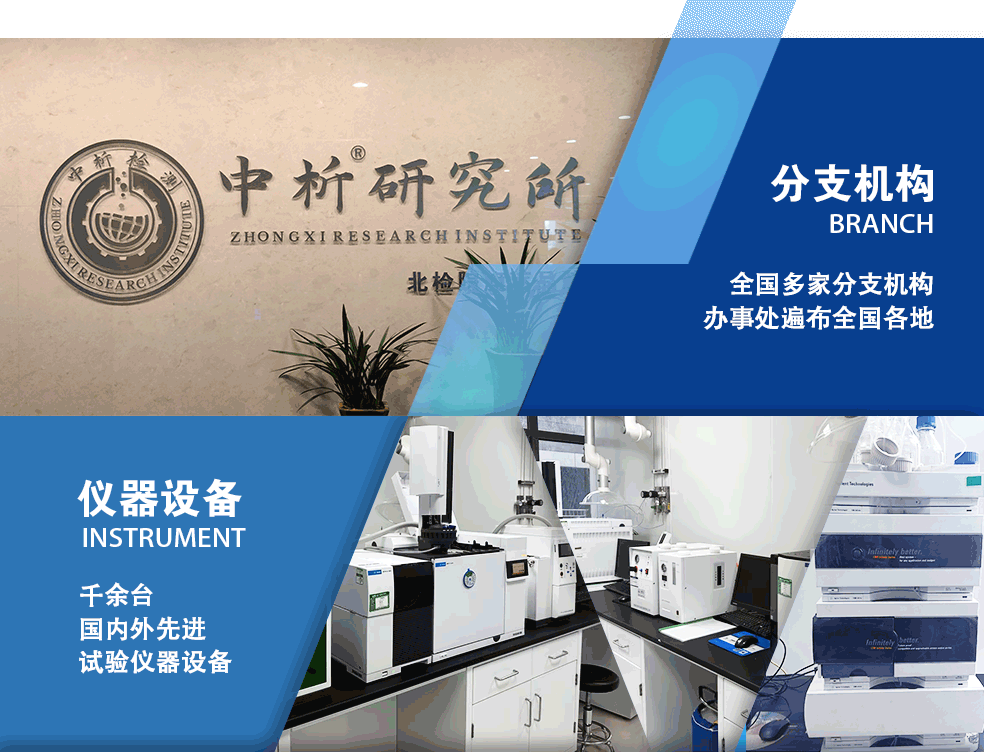