失效分析检测
发布时间:2025-04-19
失效分析检测是通过系统性技术手段追溯产品失效根源的关键流程。其核心在于结合材料学、力学及微观表征技术,准确识别断裂模式、腐蚀机理或功能退化原因。重点涵盖失效模式判定、缺陷溯源定位及损伤程度量化三大技术环节,需严格遵循ASTME2332、ISO17405等国际标准执行。
注意:因业务调整,暂不接受个人委托测试望见谅。
检测项目
机械失效:包含疲劳断裂、过载断裂、应力腐蚀开裂等12类断裂模式判定
材料劣化:涵盖晶间腐蚀、氢脆失效、蠕变损伤等9种材料退化机制分析
表面损伤:涉及磨粒磨损、接触疲劳、微动磨损等7类表面失效诊断
电子器件失效:包括电迁移、静电击穿、热载流子效应等5种半导体失效机理研究
功能退化:针对密封失效、润滑失效、传导性能衰减等6种系统级故障溯源
检测范围
机械装备领域:齿轮箱/轴承/涡轮叶片/压力容器等关键部件失效诊断
电子元器件类:PCB板/芯片封装/连接器/继电器触点失效解析
汽车零部件组:发动机缸体/变速箱齿轮/制动系统组件故障溯源
航空航天件:航空紧固件/发动机叶片/舱体结构件损伤机理研究
医疗器械类:人工关节/手术器械/植入物生物相容性失效评估
新能源器件:锂电池隔膜/燃料电池双极板/光伏组件老化分析
检测方法
宏观断口学分析:采用体视显微镜进行断口形貌三维重构(50-1000倍)
微观表征技术:运用SEM-EDS开展微区成分分析与形貌观测(最高30万倍)
晶体结构解析:通过EBSD获取晶粒取向分布及织构演变数据
力学性能追溯:采用显微硬度计进行HV0.01-HV50梯度硬度测试
化学组分检测:应用GD-OES进行元素深度剖面分析(精度达ppm级)
残余应力测试:运用X射线衍射法测定表面应力分布(精度±20MPa)
热力学模拟:通过DSC/TGA分析材料相变温度及热稳定性参数
故障树分析(FTA):建立多级故障逻辑模型进行系统性归因推演
检测仪器
场发射扫描电镜:配备EBSD和CL探测器,实现纳米级形貌-成分-晶体结构联测
聚焦离子束系统:可进行亚微米级截面制备与三维重构分析
X射线光电子能谱仪:表面化学态分析深度分辨率达1nm
原子探针层析仪:实现原子尺度三维成分分布重建(空间分辨率0.3nm)
激光共聚焦显微镜:具备3D表面轮廓重建功能(垂直分辨率10nm)
高频疲劳试验机:载荷范围±25kN,频率可达200Hz的动态性能测试
原位力学测试系统:集成SEM的纳米压痕仪(载荷分辨率10nN)
红外热像仪:温度灵敏度0.03℃,用于热失效过程实时监测
检测服务范围
1、指标检测:按国标、行标及其他规范方法检测
2、仪器共享:按仪器规范或用户提供的规范检测
3、主成分分析:对含量高的组分或你所规定的某种组分进行5~7天检测。
4,样品前处理:对产品进行预处理后,进行样品前处理,包括样品的采集与保存,样品的提取与分离,样品的鉴定以及样品的初步分析,通过逆向剖析确定原料化学名称及含量等共10个步骤;
5、深度分析:根据成分分析对采购的原料标准品做准确的定性定量检测,然后给出参考工艺及原料的推荐。最后对产品的质量控制及生产过程中出现问题及时解决。
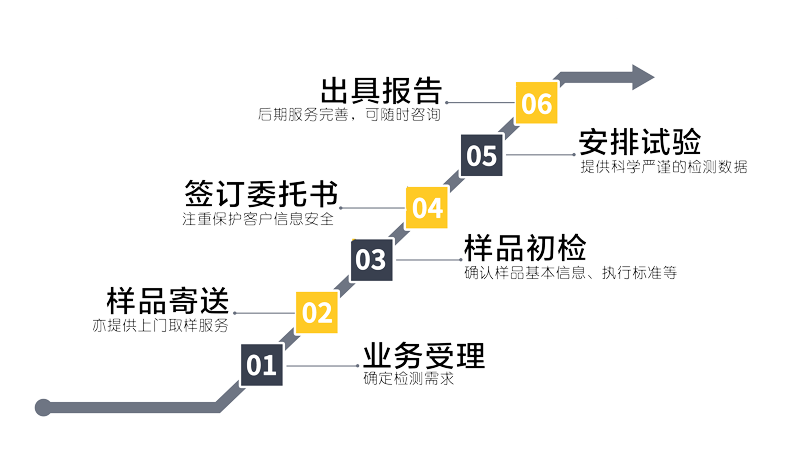
合作客户展示
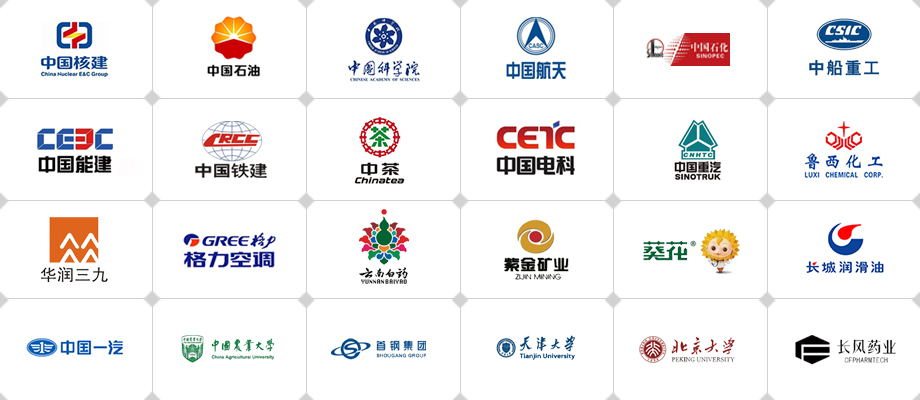
部分资质展示
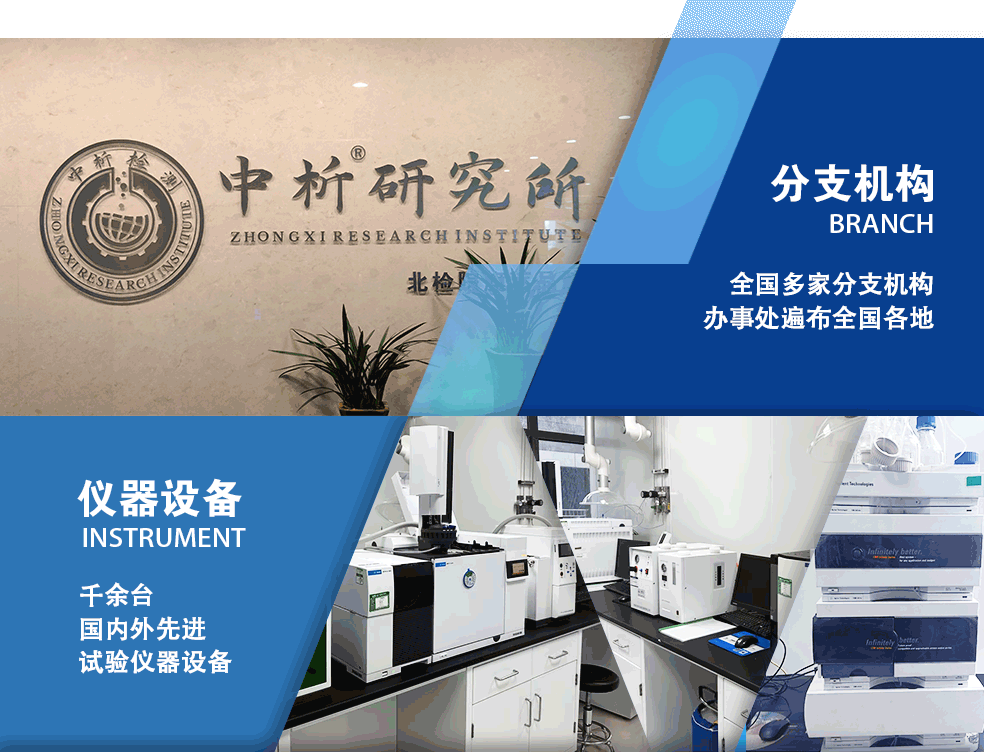